Uszczelnianie pomp w przemyśle chemicznym i wydobywczym
Czy branża chemiczna i wydobywcza potrzebują różnego rodzaju uszczelnień? Jak do tego podchodzą firmy produkujące pompy? Na te i inne pytania odpowiada Członek Zarządu firmy John Crane – Zbigniew Żyła.
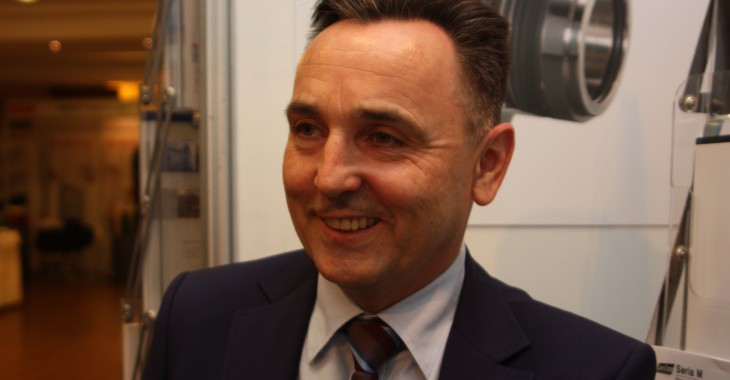
Jakiego rodzaju uszczelnienia sprawdzają się dla pomp w przemyśle chemicznym i wydobywczym? Czy branże te potrzebują innego rodzaju uszczelnienia?
W przemyśle chemicznym i wydobywczym muszą być stosowane uszczelnienia dedykowane dla tych branż.
Jak wiadomo zakres pomp jaki stosowany jest w tych przemysłach jest bardzo szeroki. W większości prostych aplikacji stosujemy uszczelnienia pojedyncze, współcześnie są to najczęściej konstrukcje cartridge’owe, czyli takie w których wszystkie elementy połączone są poprzez zwartą obudowę. W odróżnieniu od uszczelnień komponentowych, niejako składanych wewnątrz pompy, zapewniają szybki i bezbłędny montaż.
W instalacjach chemicznych pompy wyposażane są bardzo często w uszczelnienia podwójne. Celem takich rozwiązań jest zabezpieczenie układu pompowego przed wyciekiem medium pompowanego na zewnątrz, także w sytuacji awaryjnej. Rolę buforu przyjmuje wtedy neutralna ciecz barierowa dostarczana poprzez autonomiczną instalację pomiędzy dwie pary pierścieni uszczelniających. Coraz częściej stosuje się dziś w pompach chemicznych także uszczelnienia podwójne z poduszką gazową, których budowę opracowała firma John Crane jeszcze na początku lat 80-tych. Taka konstrukcja gwarantuje nie tylko całkowitą szczelność, ale także nie powoduje zużycia kosztownych pierścieni uszczelniających.
Jeśli chodzi o przemysł wydobywczy to często mamy dodatkowo problem związany z abrazją medium, co zwiększa ryzyko szybkiego ścierania się tak pierścieni uszczelniających jak również metalowych elementów uszczelnienia. Antidotum może być zastosowanie specjalnych powłok utwardzających jak materiały cermetalowe, powłoki diamentowe, a w miejsce stali nierdzewnej specjalnych stopów i materiałów kompozytowych.
Jak przez lata zmieniały się systemy uszczelnień w pompach?
To zależy, czy mówimy o uszczelnianiu mechanicznym, czy generalnie o uszczelnianiu pomp.
Historycznie zaczęło się od uszczelniania sznurami. Historia naszej firmy, która liczy równo 100 lat generalnie jest związana z uszczelnianiem pomp. Przez pierwsze 20 lat produkowaliśmy tylko sznury do pomp, gdyż to właśnie właściciel naszej firmy Pan John Crane dopiero w roku 1938 opatentował pierwsze na świecie uszczelnienie mechaniczne, zastosowane w pompie wodnej samochodu Chrysler.
A wracając do sznurów… Mają one swoje zalety, ale posiadają niestety także wiele wad. Tzw. pakunki trzeba często wymieniać, nie można uzyskać całkowitej szczelności, co najgorsze – są wyjątkowo energochłonne a to w większości zakładów coraz ważniejszy argument aby je marginalizować. Używa się ich coraz rzadziej na korzyść uszczelnień mechanicznych. Mimo większych kosztów początkowych takich rozwiązań uzyskujemy oszczędność siły roboczej, energii, zmniejszenie zużycia elementów pompy oraz zwiększenie bezpieczeństwa obsługi i środowiska naturalnego. Uszczelnienia kontaktowe średnio pracują bezobsługowo 2-3 lata, a uszczelnienia gazowe nawet powyżej 5 lat.
Firma John Crane jest nie tylko światowym liderem w produkcji uszczelnień mechanicznych do pomp, ale dostarcza także kompletny serwis w tej dziedzinie. Jesteśmy prekursorem wdrażania w przemyśle programów podnoszenia niezawodności. W skrócie, w ramach takiego programu nie dostarczamy klientowi tylko produktu, ale niejako przejmujemy odpowiedzialność za wydłużenie okresu międzynaprawczego wszystkich objętych programem urządzeń. Wspólnie z lokalnymi służbami utrzymania ruchu, w ramach opłaty ryczałtowej, dążymy do tego, aby pompy pracowały jak najlepiej. Takich kontraktów podpisaliśmy już nas świecie ponad 170, obejmując nimi ponad 50 tys. pomp. W bieżącym roku uruchomiliśmy tego typu program także w Polsce.
Czy aktualnie przeprowadzacie nowe realizacje? Wdrażacie nowe, innowacyjne rozwiązania?
Firma John Crane należy do najbardziej innowacyjnych firm w swojej branży. Stale prowadzimy nowe projekty i przynamniej część z nich jest innowacyjna. W Polsce także stale rozwiązujemy nowe, stawiane nam przez użytkowników maszyn wirujących, zadania. Taką ciekawą aplikacją wdrożoną niedawno przez nas jest uszczelnianie wałów mieszarek popiołów w elektrowni Bełchatów. Są to maszyny, które mieszają popioły z wodą i transportują je do dalszego składowania. To było bardzo trudne zadanie ze względu na znaczne gabaryty maszyny (wał 150 mm), ryzyko dużego tzw. „bicia” wału oraz wyjątkowo ścierne medium. Zastosowaliśmy tu uszczelnienia dzielone naszej produkcji typu 37SF. Są one odporne na odchyłki promieniste i wzdłużne, a jednocześnie – dzięki ich dzielonej konstrukcji – zakładanie oraz wymiana nie wymaga demontażu maszyny.
Kolejny ciekawy projekt ostatnich miesięcy to zastosowanie uszczelnień gazowych w turbinie parowej jednostopniowej w zakładach PGNiG. Nasze uszczelnienie typ 28ST, mogące pracować w temp. powyżej 400oC, skutecznie zastąpiło pierścienie węglowe stosowane dotychczas w takich maszynach. Efektem jest kilkudziesięciokrotnie zmniejszone wydobywanie się gorącej pary z turbiny, co poprawiło bezpieczeństwo oraz efektywność. Zwrot nakładów na modernizację wyniósł w tym wypadku ok. 8 miesięcy.
Dodatkowo stale modernizujemy pompy procesowe u naszych największych klientów w kraju (rafinerie LOTOS, PKN ORLEN, Grupa AZOTY PCC, Synthos i wiele innych). Tam, gdzie funkcjonują urządzenia starszego typu, zmieniamy je na nowocześniejsze, bardziej ekonomiczne i bezpieczniejsze dla środowiska. Często, korzystając z globalnego doświadczenia firmy, podejmujemy wyzwanie tam, gdzie inne firmy rozkładają ręce.
Rozmawiała Jolanta Karpiniec
Fot.: BMP